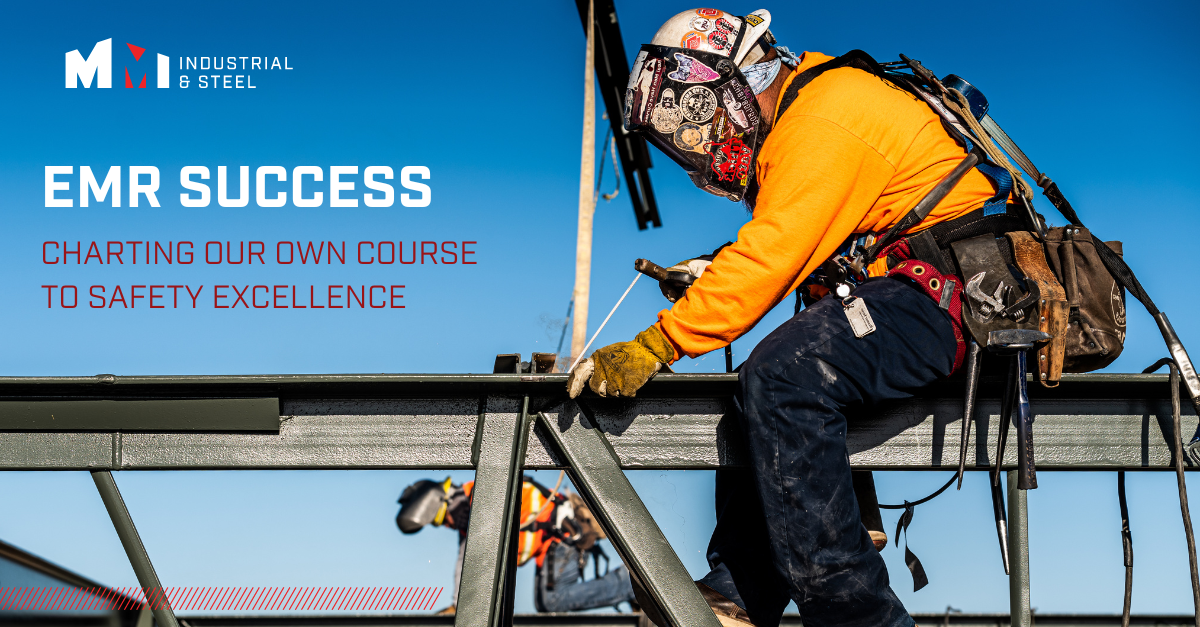
Though productivity and efficiency often take center stage in our business, MMIIndustrial & Steel has chosen to set ourselves apart through our steadfast commitment to safety excellence. For us, safety will forever remain an indispensable cornerstone of operational success. Through a metric known as EMR, or Experience Modification Rate, MMI has demonstrated a remarkable decrease, or improvement, over the course of three years, solidifying this commitment to prioritizing safety in the workplace.
The Significance of EMR
EMR serves as a pivotal indicator of a company’s safety performance relative to its peers in the industry. A lower EMR signifies better-than-average safety performance, reflecting a proactive approach towards mitigating workplace hazards and ensuring employee well-being. In essence, the decrease in EMR observed at MMI is a testament to our unwavering dedication to safety.
Breaking down the numbers, we see a clear trajectory of improvement: In the year 2021/2022, MMI Industrial & Steel saw a notable decrease of 9.52%. This positive momentum continued into 2022/2023, with a significant drop of 15.76%. Building on this success, the company achieved a further reduction in 2023/2024, translating to a noteworthy 7.81% decline in EMR. The overall percentage decrease over that three-year period totaled over29%, an impressive amount by many standards.
A Comprehensive Approach to Safety Enchancement
MMI’s path towards this achievement has been marked by consistent progress and a multifaceted approach to safety enhancement. Rather than relying on isolated strategies, we have adopted a comprehensive framework that encompasses various facets of safety management.
Central to our approach is the utilization of data-driven insights to inform decision-making and drive continuous improvement. By analyzing a spectrum of data points including incident rates, near-miss reports, safety training completion rates, safety audits, and corrective action plans, MMI Industrial & Steel gains invaluable insights into prevailing trends and potential areas for enhancement. This proactive approach enables us to identify emerging risks promptly and implement targeted interventions to mitigate them effectively.
Investment in Training, Equipment and Quality PPE
Moreover, MMI Industrial & Steel places a strong emphasis on employee training and equipment maintenance as the foundation of our safety strategy. Recognizing that well-trained employees and properly maintained equipment are essential for accident prevention, we invest significantly in comprehensive training programs and rigorous maintenance protocols. Employees are trained and certified to operate machinery, with regular inspections and maintenance routines in place to minimize the risk of accidents and injuries.
In tandem with training and maintenance efforts, MMI invests in our employees through the procurement of high-quality Personal Protective Equipment (PPE). We prioritize PPE that offers optimal protection, comfort, and durability, thereby ensuring its consistent usage among employees.
Effective Communication, Employee Empowerment, and Leadership Engagement
Effective communication is another key element of MMI’s safety strategy. Clear and consistent communication is vital to fostering a safety-conscious culture where every employee feels empowered to prioritize safety in their daily activities.To this end, the company employs a cloud-based safety forms program to streamline communication and ensure adherence to safety protocols.Additionally, a bi-weekly newsletter is utilized to distribute vital information regarding safety incidents, milestones, and areas for improvement, further advancing our culture of transparency and accountability across the organization.
Crucially, safety culture is not a top-down initiative. It is a collective responsibility shared by all team members. MMI places a premium on empowering employees to actively participate in safety initiatives and contribute to the ongoing improvement of safety protocols and practices. Through initiatives such as theSafety Observation Program and direct communication channels, employees are encouraged to provide feedback and suggestions for enhancing safety measures further.
Leadership engagement also plays a pivotal role in shaping the safety culture at MMIIndustrial & Steel. The company's leadership team is actively involved in safety initiatives, with roles and responsibilities reorganized to place a greater emphasis on safety leadership. Advanced training programs, such as OSHA30 and Rigging & Signaling, equip supervisors and key personnel with the necessary skills to uphold safety standards effectively.
To ensure that safety protocols and practices evolve in tandem with operational dynamics, MMI adopts a proactive approach towards continuous improvement. Our safety team is embedded within each project, from the pre-qualification phase to project completion, allowing the company to anticipate potential safety hazards and tailor training programs to specific project requirements.
Setting a Benchmark for Safety Excellence
MMI Industrial &Steel's progress towards safety excellence represents a holistic approach to safety management, encompassing data-driven insights, employee empowerment, effective communication, and continuous improvement. By prioritizing safety asa fundamental part of business and integrating it into every aspect of our operations, we not only achieve remarkable safety standards but also set a benchmark for excellence in the industrial and steel manufacturing industry.