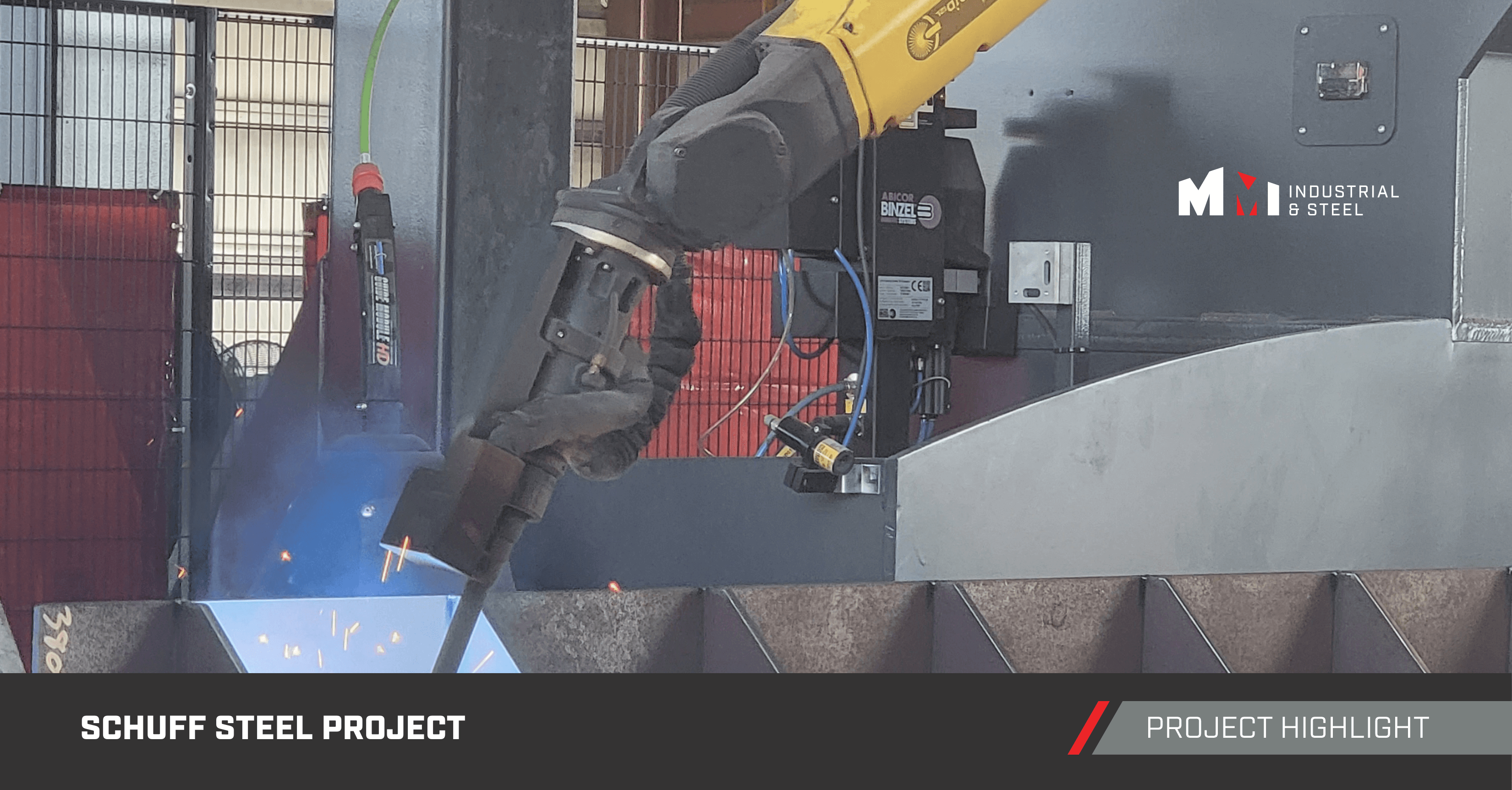
Schuff Steel, an Arizona-based company, recently contracted with MMI Industrial & Steel on a fabrication project which included 28,286 lbs. of steel. The general scope of work was bent plate with 336 gussets in total. Upon analyzing the sequences, MMI determined that 18,851 lbs. would be released for production and welded using AGT BeamMaster. This robotic welder is a state-of-the-art automation machine that increases fabrication throughput and quality. The weld inches on this job were higher than normal, which is optimal for the robot welder.
The project allowed us to innovate our production strategy with the robot. We created internal solutions for smaller assemblies which normally would not be a candidate for the robot due to size restrictions. As a result, we executed over 9,200 inches of weld for this job. This enhanced the shop’s capabilities quite nicely, as operators could focus on other more pressing tasks while the AGT BeamMaster completed the program. Furthermore, the program selected for this job completed 100% of the welds indicated on the drawings, removing the time for touchups, or finishing assemblies.
The quality on this project is worth noting. The AGT BeamMaster has a significant advantage over traditional welding because it can quickly rotate beams and verify welds. We know what welds will be missed before we even run the program. This allows us to catch bad fit-ups where a plate was missed during the fit-up stage and immediately correct it. Though this rarely occurs, it makes field installation issues a less common problem and increases quality metrics for the fabrication shop.
"The BeamMaster has helped MMI become better by introducing newer technologies, embracing change, and finding ways to work harmoniously with the machinery of tomorrow. This isn’t a tool to replace workers, but rather a tool to increase the overall output for the tedious tasks.
With the AGT BeamMaster, we can ensure the quality of the weld is consistent throughout a project; whereas, with manual welding, things such as fatigue, positioning, and experience can all negatively affect weld quality”, says Joshua Dyer, Automation Lead for MMI Industrial & Steel.