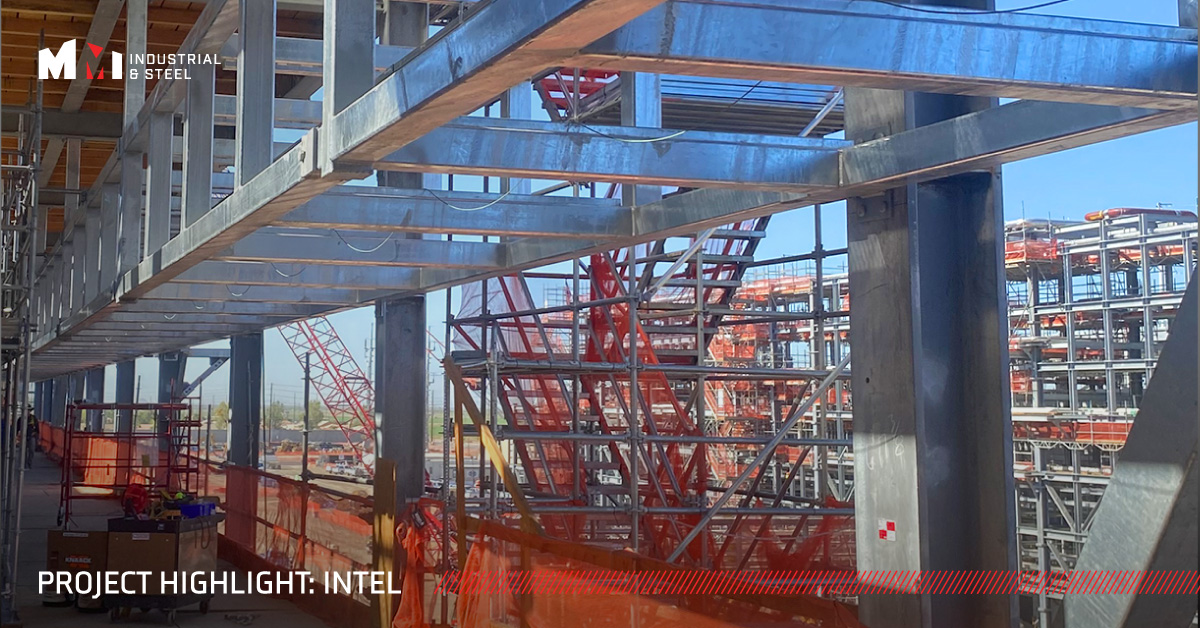
At MMI Industrial & Steel, we take pride in tackling complex, large-scale projects with precision and dedication. Our recent work with Intel at the 52.2 Fab Building is a testament to our ability to excel this type of work, executing intricate installations while navigating challenging conditions.
This project involved the erection and installation of thousands of feet of Unistrut and HSS racking to support a mix of utility delivery systems. Although the project presented many unique challenges, including intricate installations and the need to coordinate with multiple trade partners, our team successfully completed the installation, overcoming obstacles and exceeding client expectations.
Project Scope and Objectives
MMI Industrial & Steel was contracted by Hoffman and Jacobs Engineering to install thousands of feet of Unistrut racking and HSS racking throughout the Intel 52.2 Fab Building. The scope included both ceiling-mounted and floor-mounted systems, strategically placed to support various utility delivery systems. Our teams worked across the entire facility, often in highly congested areas, which required careful coordination with other trade partners.
One of the critical aspects of this project was our role in identifying and resolving design clashes, system conflicts, and field quality issues. Unlike traditional blueprint installations, our work on this project was similar to an "As-Built" system approach. This meant that our teams were responsible for identifying problems in real time, and then reporting back to Hoffman and Jacobs with potential repair strategies.
Challenges and Solutions
Executing this project successfully required us to navigate numerous logistical and operational challenges. Working in tight spaces with multiple trade partners meant that coordination, collaboration, and adaptability were key.
One of our biggest challenges was managing financial logistics while balancing trade partner coordination and client expectations. One way we navigated this was by identifying potential roadblocks and proactively developing contingency plans for potential disruptions involving labor and equipment. Real-time communication played a pivotal role; we kept all stakeholders informed of all situations so decisions and adaptations could be made swiftly.
This project also tested our team’s resilience in more ways than one. We had to handle conflicting data, tight deadlines, and evolving work conditions, often on a daily basis. Our field teams demonstrated remarkable problem-solving abilities, using resources efficiently and minimizing delays. Meanwhile, our office staff diligently managed inventory requests, RFIs, and submittals, keeping operations seamless despite the fast-paced environment.
Innovative Techniques and Technologies
While advanced tools and technology play a significant role in our industry, the most valuable asset on this project was our commitment to strong interpersonal relationships and clear communication.
Success strategies on this project included:
- Daily foreman reporting to track measurable progress
- Prioritizing alignment between ground teams and project leadership
- GF/QAQC teams partnering to audit progress and maintain quality standards
- Setting simple, well-defined expectations
- Using clear, concise language in all communication
Strategies like these allowed our teams to stay focused and efficient, and made it crystal clear that all project objectives were being met.
Key Milestones and Achievements
One of the most significant achievements of this project was recovering our schedule despite inheriting a time deficit. The scale of our work required intense effort, with teams working in demanding shifts of 72/72/60-hour weeks over a six-week period to help us catch up.
Thanks to our collaboration strategies, determined work schedule, and early identification of potential delays, we not only met our deadline but finished a week ahead of schedule.
Client Satisfaction and Lasting Impact
MMI measures the success of each project by client satisfaction. While we are proud of the fact that our teams completed this project in a timely manner, we are even more proud of the positive feedback we received from the client.
Our commitment to professionalism, safety, and cleanliness stood out, earning high praise from Hoffman’s management, safety officers, and floor superintendents. The client specifically commended our team’s approachability, adaptability, and ability to respond swiftly to schedule changes or priority adjustments. Through this project, we have forged strong relationships and proved ourselves valuable partners, setting the stage for future collaborations.
The 52.2 Fab Building project was a landmark achievement for MMI Industrial & Steel, showcasing our expertise in managing large-scale, high-stakes installations. From meticulous planning and proactive problem-solving to seamless collaboration with numerous trade partners, our team demonstrated what it means to deliver excellence under pressure. As we continue to push the boundaries of industrial and steel installation, MMI remains committed to innovation, efficiency, and client satisfaction.
Learn more about MMI’s hard-earned reputation as a trusted partner in the industry, or read more about other challenging projects MMI has completed. Ready to start your own project? Contact us today.