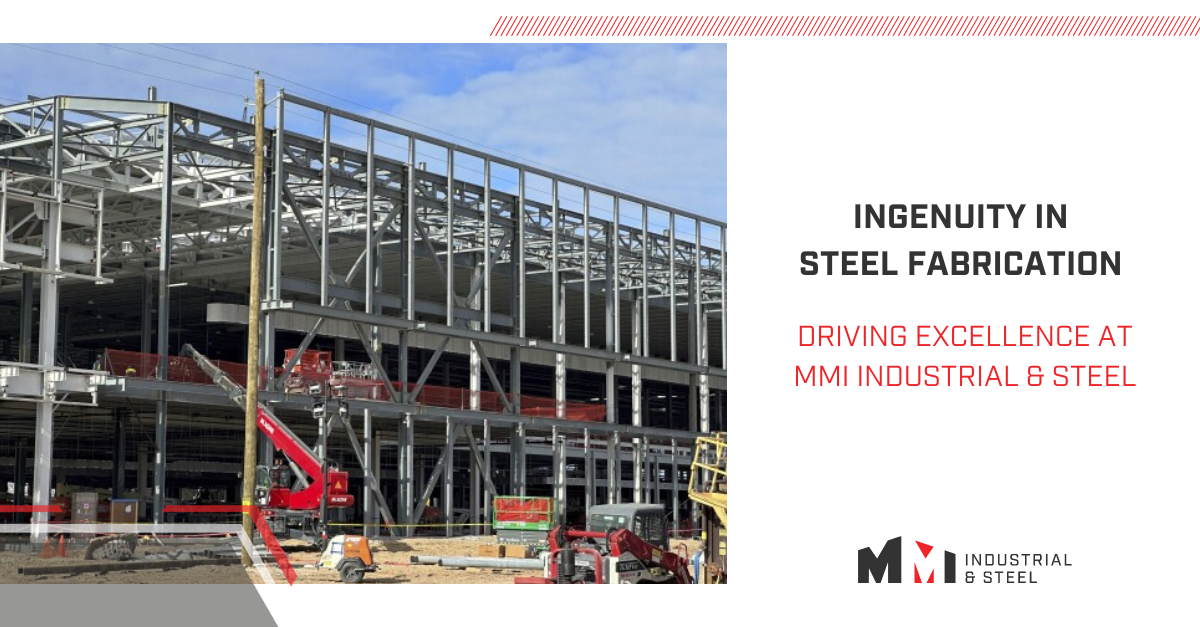
At MMI Industrial & Steel, our commitment to excellence is built into the foundation of who we are as a company. It's a driving force behind every project we undertake. As leaders in the steel fabrication industry, we continually strive to push the boundaries of what's possible through innovation, precision, and a relentless pursuit of quality. Through recent advancements in steel fabrication techniques, we have been able to elevate our capabilities, delivering exceptional results while prioritizing efficiency and the safety and wellbeing of our crews.
Recent Innovations
One of the most recent and significant innovations at MMI is the adoption of cutting-edge technology such as the Voortman V310 and V808, along with the AGT Beammaster welding robot. These state-of-the-art tools, alongside other specialized machinery tailored to our fabrication needs, have revolutionized our fabrication processes, allowing us to achieve unparalleled levels of efficiency, accuracy, and safety.
Project Showcase
A prime example of these innovations in action is MMI’s recent involvement in the construction of the new Hyundai Metaplant America, the automaker's first US electric vehicle plant, in Ellabell, Ga. Tasked with fabricating crucial components for the plant's infrastructure, including crane runways, we rose to the challenge with a combination of advanced technology and skilled craftsmanship.
Processing over 598,000 pounds of steel for the project, our team utilized the Voortman V310 and V808 to handle a range of fabrication tasks, from cutting and drilling to milling and bevel cutting. The precision and versatility of these machines ensured that each piece of steel met the project's exact specifications, laying the foundation for a successful build.
Assembly, although primarily manual, was executed with meticulous care and attention to detail, showcasing the expertise of our workforce. Every component was fitted together seamlessly, contributing to the overall structural integrity of the plant.
Efficiency, Accuracy, and Safety
The AGT Beammaster robotic welding system played a crucial role in the welding process, enabling us to achieve consistent, high-quality welds across the project's numerous trusses and beams, gusset plates, angle braces, and bent plates. By leveraging robotic precision, we were able to optimize efficiency while adhering to stringent welding standards, ultimately saving time, and reducing the risk of errors.
Throughout the implementation of these innovative techniques, we encountered and overcame various challenges. From ensuring seamless integration of manual and automated processes to maintaining strict safety protocols, our team demonstrated resilience and adaptability at every step of the way.
Our involvement in work performed at the Hyundai electric vehicle plant serves a single example of our unwavering commitment to innovation and excellence in steel fabrication. By harnessing the power of advanced technology alongside the expertise of our workforce, we were able to deliver exceptional results that exceed our client's expectations.
At MMI Industrial & Steel, our dedication to pushing the envelope in steel fabrication techniques ensures that we remain at the forefront of the industry. The success of projects like the Hyundai plant highlights our commitment to innovation, precision, and excellence in everything we do. As we continue to embrace new technologies and refine our processes, we remain steadfast in our mission to safely deliver superior quality and value to our clients.